Low-Loss Optical Fiber Manufacturing for Optoelectronics in Telco Industry
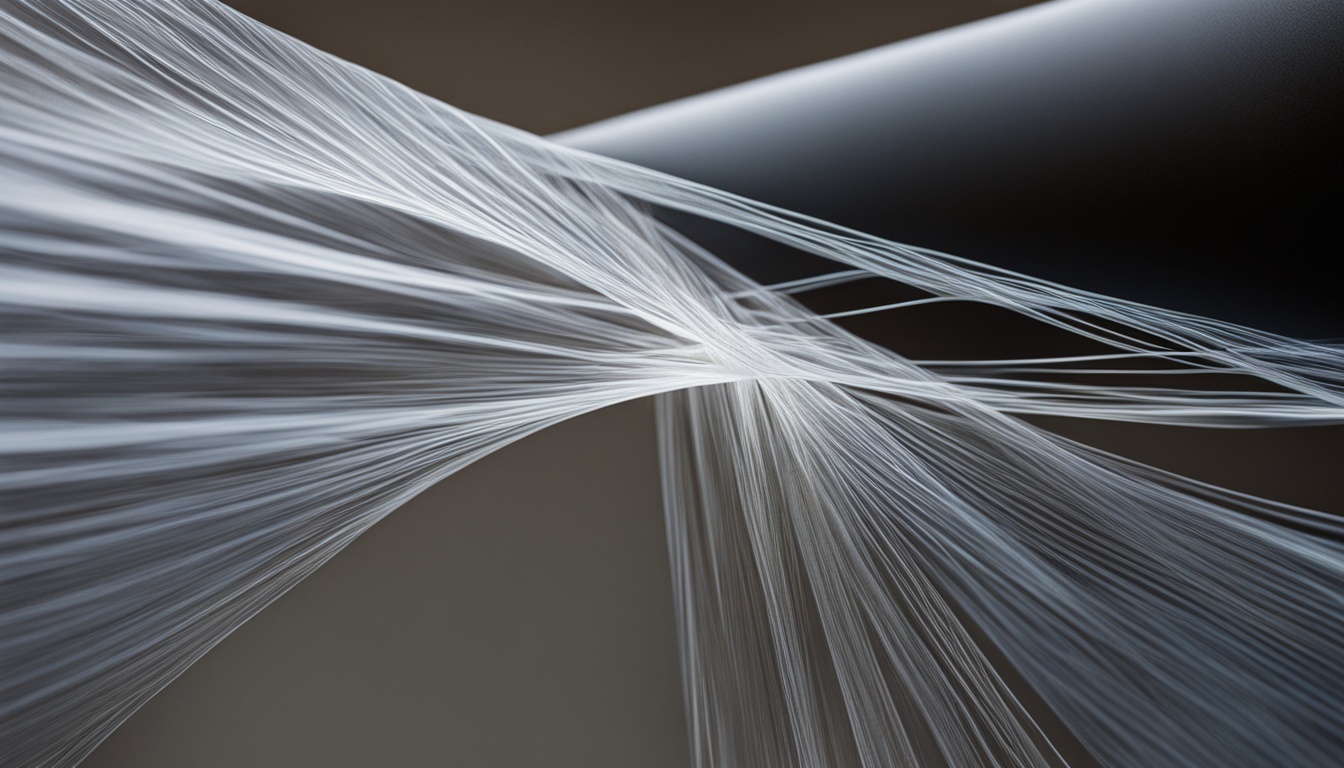
Optical fibers are at the heart of global communication networks, with yearly production exceeding 400 million km. They are particularly vital in submarine cables, needing low-loss properties for efficient transmission over vast distances. A groundbreaking achievement by Sumitomo Electric Industries was the introduction of the Z Fiber, which boasts an unprecedentedly low 0.14 dB/km transmission loss. This development, along with others such as the Z-PLUS Fiber 150, signals a strong dedication to advancing communication technology. They focus on reducing transmission loss and nonlinearity, significantly improving the effectiveness of long-distance and trans-oceanic communications.
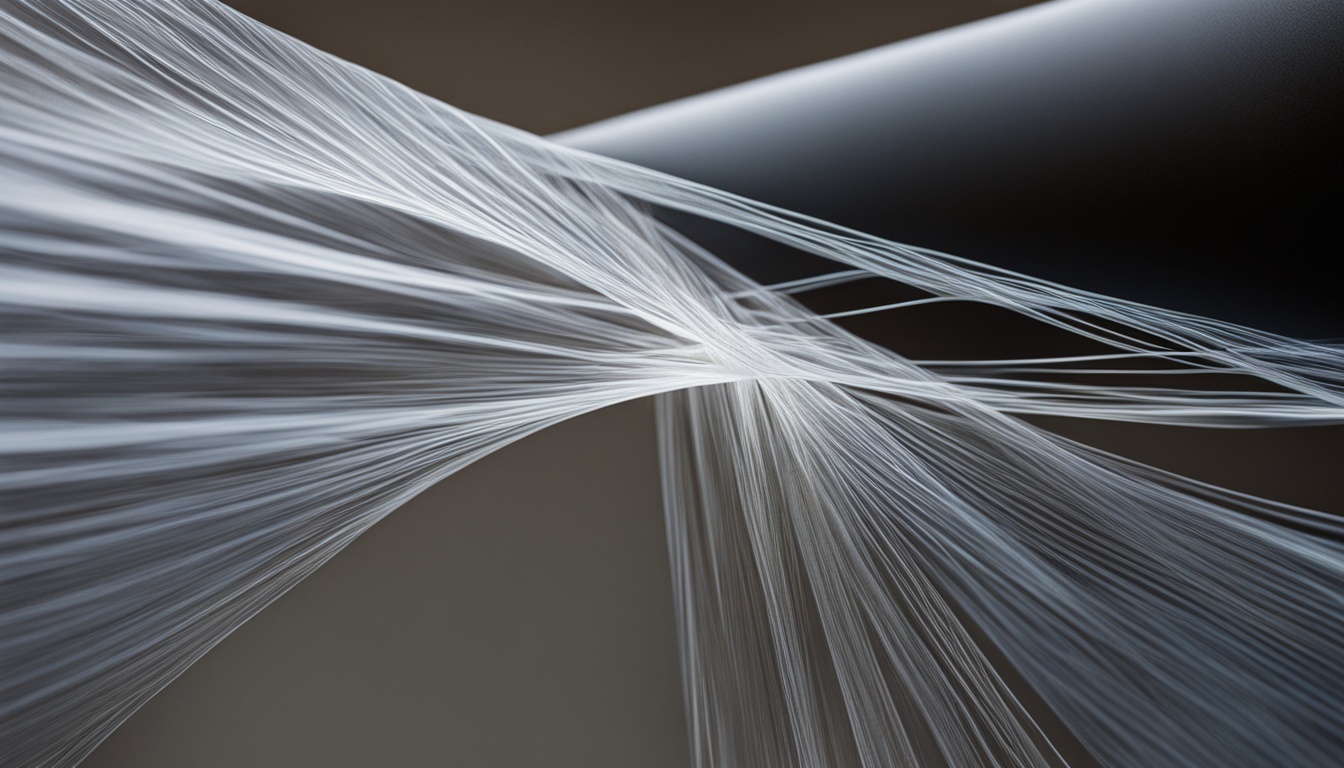
Key Takeaways
- Optical fibers are vital to global communication, with over 400 million km produced yearly.
- Sumitomo Electric leads with its Z Fiber innovation, reaching a low transmission loss of 0.14 dB/km.
- Low-loss fibers are essential for submarine cables, demanding minimal transmission loss and nonlinearity.
- The development of advanced fibers like Z Fiber and Z-PLUS Fiber 150 indicates ongoing improvements in communication technology.
- Efficient low-loss optical fibers are pivotal to the success of long-distance, trans-oceanic communication networks.
Introduction to Low-Loss Optical Fiber Manufacturing
The foundational advancement of optoelectronics relies deeply on the inception of low-loss optical fibers, a principal shift from traditional practices. Previously, infusing fibers with materials like TiO2 and GeO2 was standard. However, the paradigm changed with the introduction of a pure-silica core fiber setup. This methodology notably mitigated transmission losses, marking a crucial turn in the industry’s trajectory.
In the 1980s, Sumitomo Electric surged to the vanguard by unveiling the pure-silica core fiber design through a patented approach. This pioneering work in fiber optics revolutionized manufacturing norms, substantially lowering optical transmission losses. Consequently, it revolutionized the operational capacity and efficacy of optoelectronics apparatuses and systems.
The renowned Z Fiber, an innovation pioneered by Sumitomo Electric, epitomizes these engineering strides. Employing superior materials and stringent manufacturing protocols, it achieves drastically diminished transmission losses, thus ameliorating the efficiency and dependability of semiconductor equipment. These technical advancements drive the optoelectronic sector, ensuring incessant evolution and broader industrial applications.
The Importance of Low-Loss Optical Fibers in Communication
Within our contemporary epoch, the significance of low-loss optical fibers in communication is paramount. These fibers facilitate the transmission of data across large spans with trifling signal weakening. They serve as the foundation of our digital society, underpinning its infrastructure extensively.
Global Production Scale
The global optical fiber production scale has escalated, rendering these fibers pervasive in our interconnected globe. Their broad application highlights their essential support for multiple digital functions. Sumitomo Electric Industries, among the industry pioneers, generates millions of kilometers of these fibers yearly, meeting the ever-growing global requisites.
Reducing Transmission Losses
The quest to decrease transmission loss reflects a critical breakthrough in enhancing optical fiber efficacy and output. Such a stride not only boosts the application potential of these fibers but also curtails energy dissipation. Essential for contemporary optoelectronics and communication realms, refined optical fibers that limit transmission losses represent a sustainable choice for upcoming infrastructure needs.
Historical Development of Pure-Silica Core Fibers
The development of pure-silica core fibers fundamentally altered the field of optoelectronics. Charles K. Kao, in 1966, conducted pioneering work. His efforts laid the groundwork for substantial improvements in optical fibers, initially focusing on decreasing transmission loss. By 1970, these efforts had already diminished loss to 17 dB/km, signifying a pivotal achievement in the area.
By 1979, the field showed further advancement. Researchers managed to reduce loss dramatically, achieving a milestone of 0.20 dB/km. Consequently, this feat was paramount for establishing efficient long-distance communications, fueling the momentum in the optoelectronics sector.
Initial Innovations and Advances
Early on, the pursuit of lower transmission loss remained a central objective. Progress was evident as by 1979, the pure-silica core technology had reached a new level, with transmission loss reduced to 0.20 dB/km. This development proved crucial, rendering previously arduous long-distance communication efforts more manageable.
Key Milestones in Optical Fiber Technology
The subsequent phase witnessed significant breakthroughs, especially due to Sumitomo Electric's initiatives. Their groundbreaking efforts in the reduction of transmission loss to a remarkable 0.154 dB/km were pivotal. Such achievements elevated the performance of optical fibers in strenuous settings, such as submarine cables, inaugurating a new chapter in the evolution of optical fiber technology.
Z Fiber and Its Evolution
Z Fiber is at the cutting edge of Sumitomo Electric's optical fiber pursuits. Notably, this low-loss PSCF caters to the challenging needs of submarine optical cables. It has become a forerunner in the industry. The journey of Z Fiber is characterized by remarkable improvements, most notably the birth of the Z-PLUS series.
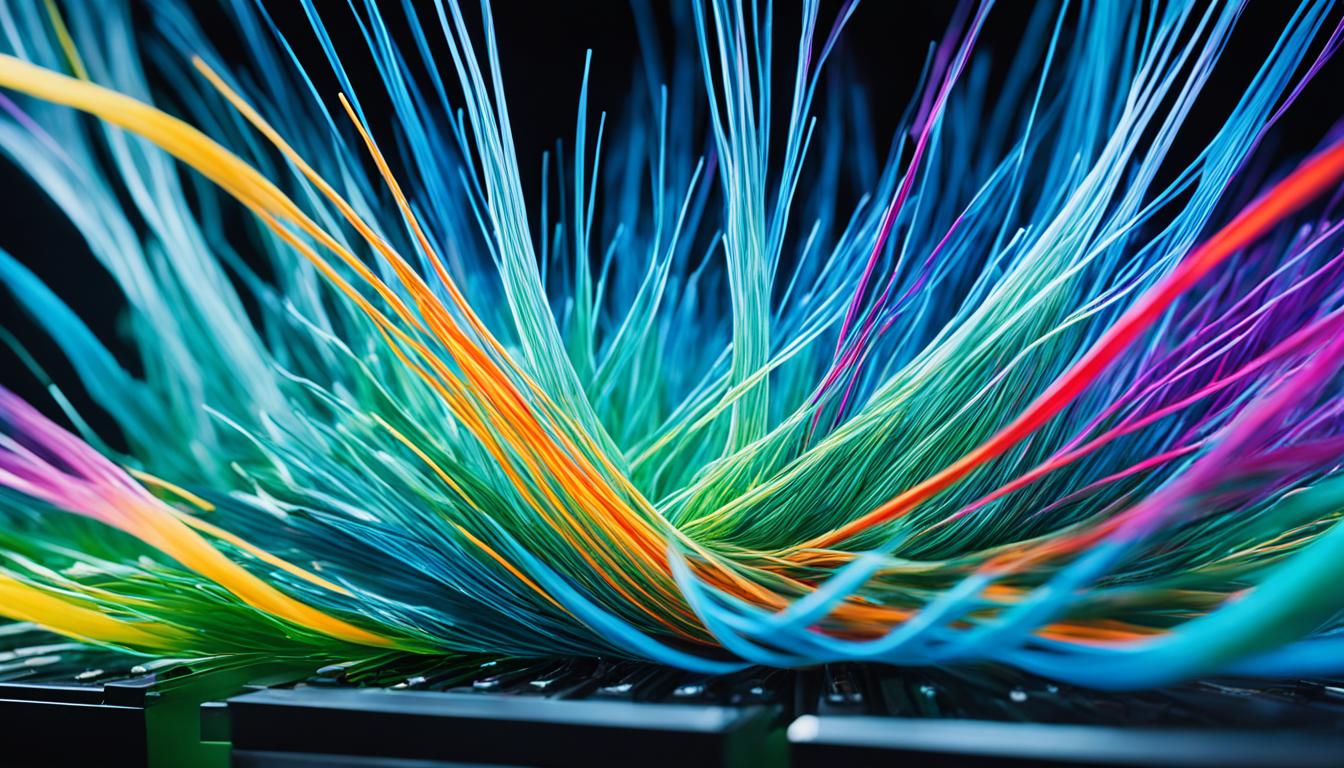
The Z-PLUS series represents a leap forward. It accommodates larger effective core areas, critical for high-power signal transmission in optoelectronic systems. Z Fiber's evolution marks a key stage in advancing silicon-on-insulator technologies, vital for cutting-edge communication systems.
Sumitomo Electric's dedication to Z Fiber's enhancement is evident. The company focuses on enlarging effective core areas, improving communication reliability over vast oceanic stretches. Applications range from telecommunications to underpinning global internet infrastructure, highlighting Z Fiber's pivotal role in cutting transmission loss and enhancing efficiency.
Z Fiber's voyage highlights Sumitomo Electric's relentless quest for optical fiber excellence. It underlines their commitment to innovation in optical fiber technology. Such persistence ensures their profound impact on the field of optoelectronics and the submarine optical cable sector.
Breakthrough in Ultra-Low Loss Optical Fibers
The introduction of ultra-low loss optical fibers has marked a substantial advancement in the field of optoelectronics, establishing unprecedented benchmarks in transmission efficacy. Sumitomo Electric is at the forefront, pioneering these breakthroughs and attaining unmatched levels of performance in optical fiber technology.
Achieving 0.14 dB/km Transmission Loss
Sumitomo Electric's accomplishment in reducing transmission loss to a mere 0.14 dB/km is truly groundbreaking. This feat underscores their dedication to innovation, elevating optical fiber technology's performance beyond prior limitations. It enables enhanced efficiency and dependability in long-distance data transmission. Through these ultra-low loss optical fibers, Sumitomo Electric enhances global communication networks by minimizing signal attenuation.
Sumitomo Electric's Innovations
Sumitomo Electric is continuously innovating in the optoelectronics realm, manifesting in the development of ultra-low loss optical fibers featuring a pure-silica core. These fibers exhibit significant enhancements in functionality and resilience, addressing the exacting requirements of contemporary communication infrastructures. The firm's unwavering commitment to research and development has not only established it as an industry leader but has also consistently provided solutions that reduce transmission loss and enhance fiber efficacy.
These strides not only propel current technologies but also lay the foundation for future innovations in optoelectronics, assuring that ultra-low loss optical fibers remain pivotal in the evolution of global communication infrastructure.
The Manufacturing Process of Optical Fibers
The creation of optical fibers is a labyrinthine process, demanding meticulous attention at every step. It all begins with the selection of materials of the highest purity. These materials are then subjected to advanced techniques in an effort to preserve their structure and ultimate functionality.
Materials and Initial Steps
High-purity materials are the foundation of this process. They undergo a transformation—being heated, collapsed, and sleeved—to create what is known as the preform. This preform's quality is paramount, as any flaw here will reverberate in the final performance of the fibers.
Drawing and Coating
The transformation continues with the drawing of the preform into a fiber. To ensure uniformity and optimal performance in optoelectronics, this step is particularly critical. The heated preform yields a glass fiber, which is swiftly coated with protective layers. These layers are designed to shield the delicate fiber from the detrimental effects of its environment.
Final Testing and Quality Assurance
Once the fiber is drawn and coated, a series of stringent tests await. These evaluations are designed to confirm the fiber's structural soundness and its transmission capabilities. Only fibers that exceed rigorous quality benchmarks are allowed further into applications within the advanced optoelectronic field.
Comparing Optical Fibers with Traditional Copper Cables
In the domain of optoelectronics, the discourse surrounding optical fibers vs. copper cables symbolizes the ongoing expansion of communication technologies. Optical fibers are unparalleled in their ability to transmit data at exceptionally high rates while conserving energy efficiently. This attribute, crucial for our modern communication network infrastructure, distinguishes optical fibers as a key technology.
Optical fibers clearly surpass traditional copper cables in data transmission velocities and bandwidth. This superiority arises because copper cables face a decline in performance as frequencies increase, due to the skin effect. Conversely, optical fibers sustain the integrity of high-speed data with minimal signal loss, positioning them as foundational in applications that necessitate rapid and dependable data exchanges.
Furthermore, the energy efficiency of optical fibers is particularly notable. Their lower signal attenuation allows data to traverse long distances without frequent signal enhancements. This quality aids in energy conservation, thereby lowering operational expenditures notably.
Additionally, optical fibers exhibit significantly less susceptibility to electromagnetic interference than copper cables. This quality is a boon for sectors that demand high system dependability, such as those implementing semiconductor equipment and delicate electronic apparatus. Enhanced reliability and performance result from optical fibers’ reduced interference issues.
When considering optical fibers vs. copper cables, the decision rests on the application's particular needs. Optical fibers, with their unmatched rapidity, energy efficiency, and data integrity, present a compelling choice for advanced optoelectronics and communication environments.
Advanced Testing Methods for Optical Fibers
Ensuring the reliability of optical fibers is paramount for their use in crucial optoelectronics. This endeavor requires thorough fiber optic testing techniques. These are crafted to check the fibers’ durability and performance across various scenarios.
Mechanical stress testing is pivotal for fiber optics evaluation. They imitate real-world stresses like bending, stretching, and crushing. Verifying fibers’ resilience against such stresses is crucial. It ensures their longevity and reliability. The following outlines the main tests:
For optoelectronics, precision and reliability are of utmost importance. These tests are instrumental in ensuring that the fibers adhere to rigorous industry measures. Every fiber optic testing methodology yields critical insights. They guarantee that the products remain reliable in adverse settings. Therefore, these assessments aid in expanding the possibilities of optical communication and optoelectronics.
Innovative Applications in Optoelectronics
The realm of optoelectronics burgeons with the progress in fiber optics. These advancements catalyze the birth of novel applications, driving pioneering advancements in disparate domains.
Photonic and Quantum Optics
Optical fibers, via photonic optics and quantum optics, elevate precision and efficacy. Tapered fibers, with their capacity for strong confinement and expansive evanescent fields, underpin superior nonlinear effects. Such capabilities are instrumental for the evolution of more advanced optical setups.
Optical Sensing and Spectroscopy
Advancements in optical sensing and spectroscopy usher in greater accuracy and dependability. Thanks to evolved optical fibers, sensors achieve heightened precision, leading to significantly more trustworthy measurements and observations.
Light-Matter Interaction
Interfacing light and matter constitutes the cornerstone of several optoelectronic innovations. Advanced fiber optics newly enable profound and efficient light-matter interactions. This, in turn, powers discoveries across multiple technological sectors.
Customization and Length Optimization of Fiber Optics
Fiber optics customization pertains to the detailed design of optical fibers for specific needs. This process involves adjusting fiber length to minimize loss and achieve optimal performance. Such customization makes them suitable for various intricate applications.
Tailoring Fiber Optics for Specific Applications
Customizing fiber optics is paramount for specific industrial and device needs, especially in silicon wafer applications. This tailored approach maximizes optical properties, boosting efficiency and effectiveness in severe applications.
Adiabaticity and Minimizing Loss
For minimal loss, adhering to adiabaticity principles in fiber optic production is crucial. It ensures a smooth transition of the fiber's traits to maintain high transmission. This precision is vital for applications that demand flawless light delivery, meeting the stringent requirements of modern semiconductor devices.
Conclusion
The evolution of optical fiber technology, underpinned by continuous innovations, has significantly redefined the optoelectronics domain's paradigm. With the pioneering work of entities such as Sumitomo Electric and the meticulous manufacturing methods employed to create low-loss optical fibers, the sector has witnessed unparalleled growth. These fibers, noted for their minimal transmission loss attributes and their enhancement of communication effectiveness, delineate the very backbone of global communication infrastructure.
Looking towards the future, the salience of low-loss optical fibers in the communication sector is set to increase. The optoelectronics field is poised at the brink of a major revolution, underscored by the transformative capacity of sophisticated fibers on data transmission. Availing themselves to a realm of applications, from underwater communication lines to accelerated internet services, further research and development envision a horizon glinting with streamlined and dependable communication networks.
Sumitomo Electric's consistent pursuit of excellence, manifested through its notable explorations, highlights the sector's advancements. Their commitment not only solidifies present-day applications but also paves the path for a new phase in the optoelectronics continuum. The ongoing evolution of such fibers predicates a scenario where communication ecosystems are not only more durable but also increasingly adept at fulfilling the burgeoning needs of a digitally interconnected society.
FAQ
What makes low-loss optical fibers crucial in optoelectronics?
Low-loss optical fibers are paramount for efficient long-distance data transmission with minimal signal attenuation. They bolster the performance of communication networks, particularly in stringent settings such as submarine cables. By curbing energy dissipation and enhancing signal fidelity, these fibers are foundational.
How are pure-silica core fibers manufactured?
The creation of pure-silica core fibers commences by meticulously choosing impurity-free materials. These materials are processed through heat, collapse, and sleeving phases to configure glass fibers. Precise drawing techniques guarantee uniform fiber dimensions. An exhaustive quality monitoring process is employed to ensure the fibers' systematic integrity and superior transmission attributes.
What are some key milestones in the development of optical fibers?
Several pivotal milestones mark the history of optical fibers. Charles K. Kao's 1966 breakthrough initiated the development of low-loss fibers. By 1970, a substantial achievement was made with a 17 dB/km loss. This loss was further reduced to 0.20 dB/km in 1979. Notably, Sumitomo Electric elevated the industry’s standards with a milestone 0.154 dB/km loss, continually improving to an unparalleled 0.14 dB/km.
What is the significance of Sumitomo Electric's Z Fiber?
Sumitomo Electric's Z Fiber marks a significant advancement in low-loss optical fiber technology tailored for submarine cables. It sets a new standard with an astonishingly low 0.14 dB/km transmission loss. This achievement is emblematic of cutting-edge innovations in optoelectronics and silicon-on-insulator technologies.
How does the transmission loss of ultra-low loss optical fibers compare to traditional fibers?
The transmission loss of ultra-low loss optical fibers, exemplified by Sumitomo Electric's Z Fiber, plummets to 0.14 dB/km. This is starkly lower than what conventional fibers offer. Such a substantial reduction in loss is critical for improving the efficiency and reliability of long-range communications.
Why is customization important in fiber optics manufacturing?
Customization in fiber optics manufacturing is vital, tailoring fibers for specific applications. It focuses on optimizing length to reduce transmission loss and heightening overall performance. This aspect is key for applications demanding utmost precision, like the creation of semiconductor equipment and advanced optoelectronics.
How do optical fibers compare to traditional copper cables in terms of performance?
Optical fibers outperform traditional copper cables by maintaining signal integrity at high data velocities and offering superior energy efficiency. Copper cables falter at greater frequencies due to the skin effect. Consequently, optical fibers are the preferred medium for swift and energy-efficient data transmission in advanced optoelectronics.
What advanced testing methods are used for optical fibers?
Advanced testing methodologies for optical fibers encompass mechanical and environmental scenarios, testing them against extreme temperatures, crushing, bending, and weight variances. These procedures pinpoint potential failure nodes and assess the fibers' resilience under stress. They guarantee that the fibers adhere to exacting performance benchmarks.
What innovative applications emerge from advancements in optical fibers?
Optical fiber advancements catalyze new possibilities in optoelectronics, propelling sectors like photonic and quantum optics, optical sensing, and spectroscopy. These fibers facilitate efficient nonlinear effects and potentiate robust light-matter interactions, driving innovation and progress in these technological domains.
How is adiabaticity ensured during the fiber manufacturing process?
Maintaining adiabaticity necessitates a manufacturing process that ensures a smooth, gradual transition in the fiber's structure to mitigate transmission loss. This process is especially critical for applications requiring extreme precision, such as advanced optoelectronics and semiconductor equipment utilizing silicon wafers.
Source Links
- https://www.vse.com/blog/2024/04/25/fiber-optic-cable-manufacturing-for-optoelectronics/
- https://global-sei.com/fttx/pureadvance/specialwebsite/pdf/The First 0.14-dB per km Ultra-low Loss Optical Fiber.pdf
- https://opg.optica.org/oe/abstract.cfm?uri=oe-22-23-28427