About Ion Pump
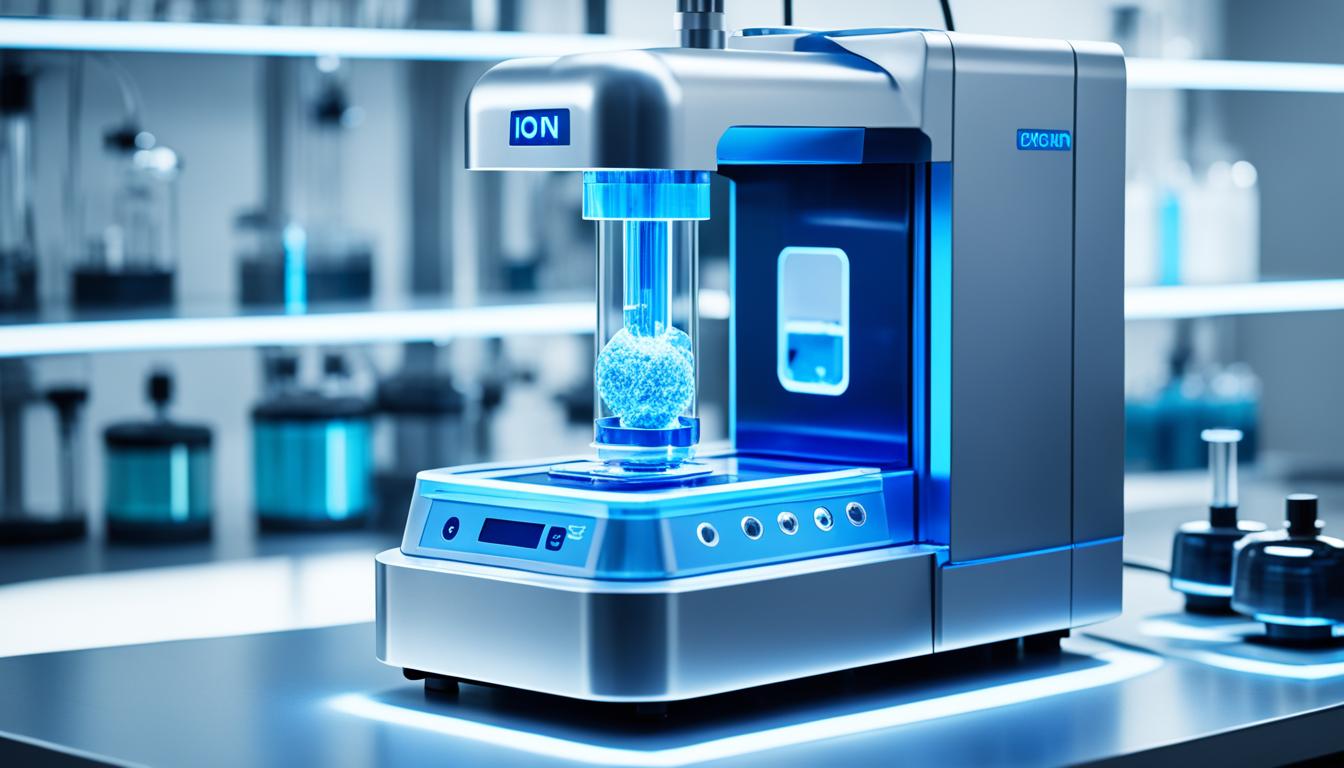
An ion pump, called a sputter ion pump, plays a critical role in achieving ultrahigh vacuum levels essential for cutting-edge technology. This innovative vacuum pump technique functions by ionizing gas molecules and employing a metal getter to sputter the ionized gas. Consequently, it efficiently removes gases from the system. A notable characteristic of ion pumps is their operation devoid of moving components, enabling them to attain remarkably low pressures, approximately 10−11 mbar. The inception of ion pumping marked a significant milestone in the history of vacuum technology. This field witnessed key advancements, notably by Julius Plücker in 1858, followed by milestones set by Varian Associates in 1957. These milestones ushered in the era of ultrahigh vacuum applications, crucial for supporting scientific research and various industrial processes.
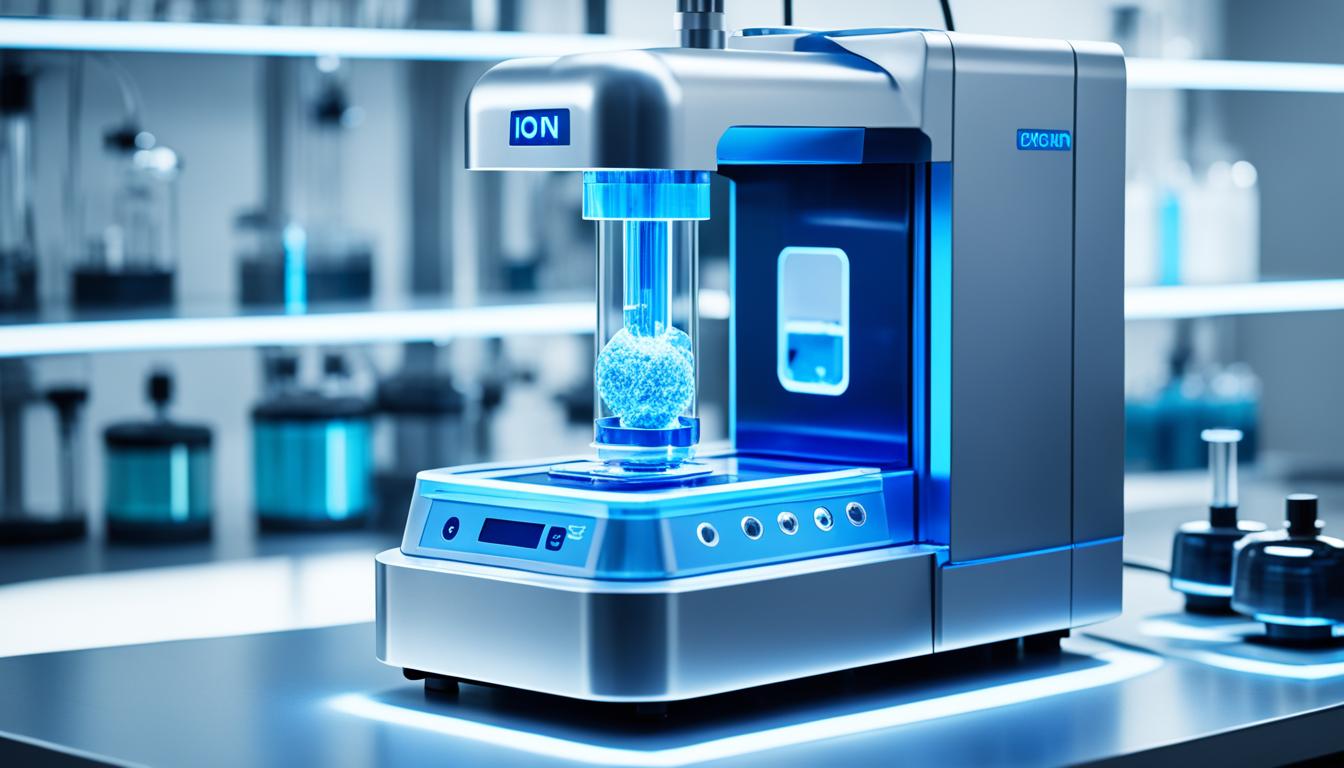
Key Takeaways
- Ion pumps, including sputter ion pumps, achieve ultrahigh vacuum levels.
- This technology works by ionizing gas molecules and sputtering a metal getter.
- Ion pumps can reach low pressures around 10−11 mbar without moving parts.
- The technique was significantly advanced by Julius Plücker and later by Varian Associates.
- Ion pumps are essential in various applications requiring ultrahigh vacuum conditions.
Introduction to Ion Pump Technology
The ion pump stands as a cornerstone within vacuum technology, especially crucial for establishing and retaining ultra-high vacuum states. This specialized apparatus operates by ionizing gas particles in an enclosed chamber. It then employs a potent electrical field to sequester these ionized particles. Consequently, it diminishes the internal pressure. Renowned for their clean operation and non-vibrational characteristics, ion pumps are vital across scientific and industrial settings.
What is an Ion Pump?
At its core, an ion pump represents a distinct variant of vacuum pump technology. It leverages the mechanisms of gas ionization and subsequent ion capture to achieve and maintain ultra-high levels of vacuum. Through the process of ionizing gas in a vacuum chamber and applying a robust electrical field, these pumps are proficient in the elimination of gases. This ensures the establishment of a pure, unwavering vacuum environment.
Brief History of Ion Pumps
Ion pump technology is indebted to the pioneering efforts of German physicist Julius Plücker during the late 19th century. His foundational work laid the essential framework for this critical technology in the vacuum domain. In 1957, significant strides were achieved by Varian Associates, who not only introduced but also patented an innovative design. This design facilitated the attainment of unprecedented ultra-high vacuum levels, marking a significant milestone in the field.
Why Ion Pumps Are Crucial in Vacuum Technology
In the realms of both science and industry, ion pumps are indispensable. They are paramount for the creation and maintenance of ultra-high vacuum conditions essential for various applications. For instance, in semiconductor manufacturing and material science research, a pristine vacuum environment is obligatory. Ion pumps play a crucial role, ensuring the exactitude and consistency needed. They stand as essential instruments in technological progress.
Working Principle of Ion Pumps
Diving into the functional core of ion pumps reveals their stalwart role in creating ultra-high vacuum settings. To grasp this, we dissect the essential mechanisms that propel their proficiency. This exploration is pivotal in understanding ion pumps' inner workings.
Penning Trap Mechanism
The cornerstone of ion pump function is the Penning trap, using magnetic and electric fields synergistically. Powered by a strong orthogonal magnetic and electric field setup, it efficiently confines and ionizes gas molecules. This design induces charged gas particles into cyclotron orbits, a technique that significantly elevates ionization rates.
Ionizing Gas Particles
Once gas molecules are trapped in the Penning trap, ionization ensues. The process is initiated by high-energy electrons that collide with neutral gas molecules. This collision generates ions and secondary electrons, initiating a cascade that swiftly transforms the gas into positively charged ions. These ions are now primed for further manipulation within the pump.
Sputtering Process
The subsequent step involves a sophisticated sputtering variant. Here, ionized particles are directed towards a titanium cathode, inducing sputtering. This action dislodges titanium atoms, which then layer the surrounding surfaces, capturing and concealing residual gas molecules. Maintaining a continuously fresh reactive surface is central. It enables the pump to sustain its efficacy by consistently trapping gas.
Types of Ion Pumps
Ion pumps, though varied in design and function, are crafted for distinct vacuum requisites. The primary types include the standard diode, noble diode, and triode ion pumps. Choosing the most suitable pump requires an in-depth understanding of each one's features and benefits.
Standard Diode Pump
The standard diode ion pump stands as a prevalent choice for broad vacuum uses. It relies on a titanium getter to ionize and confine gas particles. Esteemed for its dependability and simplicity, it fits a myriad of applications without complexity.
Noble Diode Pump
Noble diode ion pumps, featuring tantalum cathodes, are adept at eliminating inert gases. Their ability to efficiently handle gases like helium and argon adds value in applications requiring their reduction. The use of tantalum further bolsters their effectiveness and service life.
Triode Pump
Triode ion pumps excel by their design with distinct sections for sputtering and creating films. This arrangement ensures consistent gas pumping, especially for noble gases, extending the pump's lifespan. Their capability to uphold high vacuum levels for prolonged durations makes them indispensable in rigorous applications.
Applications of Ion Pumps
Ion pumps are pivotal across various scientific and industrial sectors, predominantly for their capability of generating and sustaining ultrahigh vacuum conditions. This efficiency is critical for creating environments devoid of contaminants. Such environments are imperative for conducting highly precise experiments and manufacturing operations.
Ultrahigh Vacuum Systems
Within the domain of ultrahigh vacuum systems, ion pumps function as essential elements. These systems necessitate pure vacuum levels to foster precise and dependable experimental outcomes. The methodical use of ion pumps in sustaining these conditions is paramount for a plethora of delicate applications.
Scientific Research
Within scientific exploration, the exactness of ion pumps is irreplaceable. Tools like molecular beam epitaxy and scanning probe microscopy demand exceedingly pure environments. The ultrahigh vacuum facilitated by ion pumps is essential for the integrity of these intricate procedures. It guarantees superior data and final results.
Industrial Uses
In industrial applications, particularly semiconductor fabrication, ion pumps are employed to eradicate detrimental particles. This action ensures the development of electronic elements occurs in a hygienic environment. Ion pumps play a critical role in maintaining the sterility of this essential manufacturing process.
Advantages of Using Ion Pumps
Ion pumps are frequently opted for in contexts that necessitate ultrahigh vacuum environments, given their unrivaled merits. These pumps excel in keeping the surroundings clean and oil-free. They also need little maintenance and operate without vibrations. These qualities are highly esteemed across several sectors.
Clean Operation
Clean vacuum technology is a key hallmark of ion pumps. This attribute is due to their lack of oil and moving parts. In the context of vacuum pumps, which might taint the environment, ion pumps stand out. They offer a pure vacuum space, which is essential for tasks that are highly sensitive.
Low Maintenance
The design of ion pumps is crafted to require low maintenance. This feature lowers the necessity for regular check-ups. The absence of mechanical parts slashes down on wear and tear. It also bolsters the pump's overall longevity. This results in a durable and economical option for extended operations.
Vibration-Free Performance
Ion pumps distinguish themselves with their vibration-free environments. This benefit is crucial for endeavors that rely on precision, like scientific studies and semiconductor fabrication. Their steady operation guarantees accuracy and the ability to repeatedly achieve results in both experimentation and manufacturing.
The amalgamation of clean vacuum technology, the economization on maintenance, and the provision of a vibration-free atmosphere underscores the profusion of benefits linked with ion pumps. They emerge as an optimal choice for applications demanding superior exactness.
Challenges and Limitations of Ion Pumps
Ion pumps offer significant benefits, yet face substantial limitations that hinder their operational efficiency and versatility. A key issue is their efficiency in trapping light gases, especially hydrogen and helium. The low atomic mass of these gases makes them hard to contain, exacerbating vacuum pressure difficulties.
Additionally, these pumps can only handle a certain volume of gas. As the getter material saturates over time, their ability to maintain high pumping speeds dwindles. In turn, this impacts their performance in gas-rich environments, posing challenges for sustained operation.
Their ability to sustain ultra-high vacuum conditions over prolonged durations is another significant hurdle. With the aging of the getter material, the pump's efficiency declines sharply. This situation necessitates frequent maintenance to either refresh or replace the getter material, representing a substantial operational demand.
For a comprehensive perspective on these limitations, a comparative view is instrumental:
Ion Pumps vs Other Vacuum Pumps
The field of vacuum technology has evolved significantly, yielding a spectrum of pump types tailored for distinct purposes. A critical comparison of vacuum pumps like ion models against turbomolecular, diffusion, and NEG pumps elucidates their differential efficiencies and roles under specific scenarios. This discourse serves to underline the variegated performances of these equipment.
Turbomolecular Pumps
Characterized by their eminent pumping velocities and capability to secure high vacuums, turbomolecular pumps employ a method that imparts kinetic energy onto gas molecules. By employing high-speed rotating blades, these pumps drive gas out of the chamber efficiently. Primarily useful for applications necessitating swift pressure diminution, they represent a crucial technology in vacuum sciences.
Diffusion Pumps
Conversely, diffusion pumps are esteemed for their large gas handling capacities. Utilizing a vaporized oil jet, they effectively reduce pressure within the chamber, making them ideal for tasks demanding steady vacuum conditions over prolonged durations. Their operational mechanism underscores the distinct but indispensable nature of each pump type in achieving and maintaining varying vacuum environments.
Non-Evaporable Getter Pumps
Non-evaporable getter pumps are designed to capture hydrogen and reactive gases without causing any electromagnetic disturbances. Leveraging materials such as titanium or zirconium, they adsorb and bind gases chemically. This characteristic makes them indispensable in environments where electromagnetism must remain undisturbed.
Determining the optimal pump for a vacuum system relies on a comprehensive understanding of its functional demands. Essential factors such as the need for quick evacuation, large gas capacity, or specific gas capture methods influence the choice. Extensive UHV pump comparisons are instrumental in evaluating these criteria, facilitating the selection of the most suitable pump for diverse applications. These assessments are crucial in ensuring efficient attainment of requisite vacuum levels.
Choosing the Right Ion Pump for Your Needs
Selecting the right ion pump involves understanding key factors governing vacuum needs. This includes pinpointing ideal pressure levels, gas types, and chamber sizes. Notably, companies like Agilent and Gamma Vacuum furnish varied ion pumps suited to precise contexts, underscoring the need for bespoke solutions.
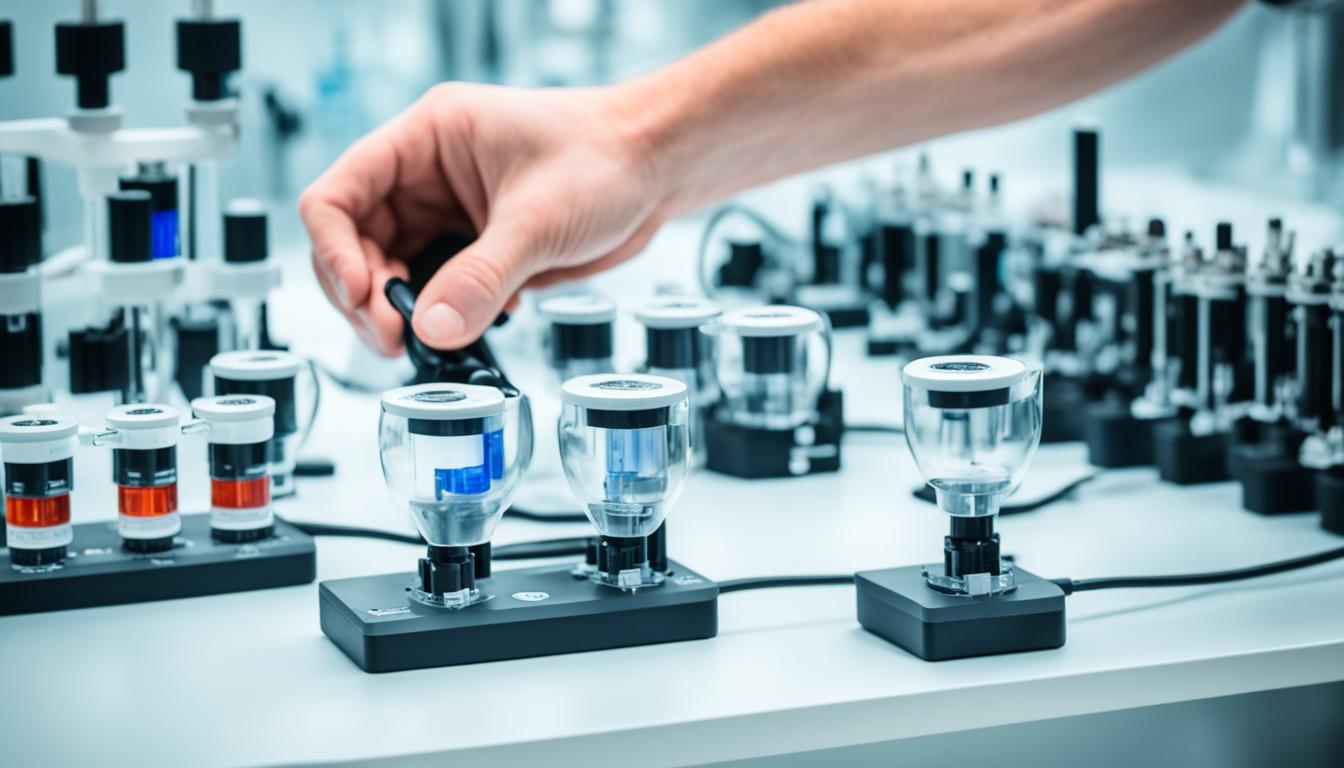
Pump efficiency stands as a critical consideration within this decision-making framework. A high-quality ion pump should meet performance needs adeptly, while ensuring durability and consistent operation. This evaluation encompasses the determination of the optimal pump type, whether standard diode, noble diode, or triode, with their distinct gas management capabilities and efficiency profiles.
This process is further enriched by the provision of tailored options from manufacturing entities. These customization avenues extend to adjustments in cathode material or structure, positively influencing applications in sectors requiring advanced precision, such as scientific exploration and industrial production.
The criticality of precise ion pump customization cannot be overstated. Tailoring configurations to specific vacuum demands is essential for ensuring ongoing pump efficiency and operational excellence within applications spanning scientific and industrial domains.
Maintenance and Troubleshooting
Ensuring optimal performance and a lengthy lifespan for your ion pump mandates a regimented schedule of maintenance and troubleshooting. We offer detailed advice for both in order to sustain high operational levels in your ion pump. Regular care is advisable to preempt common issues and maintain seamless operation.
Common Issues
Various factors may impede an ion pump’s functionality. Among these, a prevalent concern is diminished pumping velocity due to contaminants adhering to the cathode. Additionally, gas backstreaming can deteriorate vacuum integrity by facilitating the reentry of previously evacuated gases into the chamber. A systematic vigil for these complications is instrumental for sustaining ideal efficacy.
Regular Maintenance Tips
Adhering to a structured maintenance regimen is pivotal in averting considerable setbacks. The following directives can prove invaluable:
- Monitor pressure levels: Keep a close eye on vacuum pressure, noting any abrupt alterations that signify potential issues.
- Inspect the cathodes: Verify the cleanliness of titanium cathodes, rectifying any contamination promptly.
- Clean the system: Routinely purge the vacuum chamber’s internal surfaces to forestall the accumulation of detritus detrimental to performance.
- Check electrical connections: Scrutinize the integrity of all conduction points for any signs of degradation, rectifying as necessary.
Implementing these suggestions is indispensable for the efficacious operation and durability of your ion pump.
When to Seek Professional Help
Occasionally, diligent maintenance may prove insufficient, necessitating professional aid. Indications such as electrical malfunctions, anomalous auditory emissions, or substantial cathode erosion highlight the need for expert attention. In such scenarios, professionals adept at vacuum pump diagnostics and remediation are indispensable for facilitating a swift return to optimal functionality.
Future Trends in Ion Pump Technology
Ion pump technology is at a critical turning point, with research pushing for substantial advances. It focuses on improving ion pump efficacy through the development of new getter materials. The primary goal is to enhance the efficiency of ion pumps significantly. These novel materials are designed to meet the increasing needs of vacuum technology, promising better performance in harsh environments.
Moreover, a key trend is the integration of ion pumps with state-of-the-art vacuum systems. This integration paves the way for achieving ultra-low pressures and superior pumping speeds. The evolution of control systems is also anticipated, which will lead to enhanced precision and reliability for the next generation of ion pumps.
Looking to the future, ion pump innovation will pivot towards smart technologies. This shift envisions the integration of automatic diagnostics and performance enhancement features. Such advancements are vital for the sustained top-tier performance of ion pumps, ensuring their durability. With the continuous progress in vacuum technology, the scope and dependability of ion pumps will broaden, catalyzing new scientific and industrial advancements.
Conclusion
Ion pumps stand as a pinnacle in vacuum technology, fundamentally shaping the attainment and maintenance of ultrahigh vacuum environments. Introduced by Julius Plücker, their evolution under Varian Associates has propelled significant scientific and industrial strides. A retrospection on the ion pump's influence reveals their pivotal role in the evolution of vacuum technology and the push towards ultrahigh vacuum accomplishments.
Ion pumps, through a sophisticated interplay of gas ionization and sputtering, ensure a vacuum that is both clean and stable. Unlike other methods, they avoid the inherent issues of mechanical components and contaminations. Such characteristics make them indispensable in applications across the board, from semiconductor processing to cutting-edge research. Their dependability and efficiency position them at the frontier of achieving demanding purity and precision standards.
The trajectory of ion pump technology promises continued innovation, with a focus on enhanced efficiency and broader capabilities. Exploration of novel getter materials and the advancement of control systems are but a preview of the field's potential. These strides, alongside integration with complementary vacuum technologies, will sustain ion pumps' critical role in the relentless pursuit of ultrahigh vacuum limits. Consequently, ion pumps will endure as essential components in a variety of crucial applications for the foreseeable future.
FAQ
What is an Ion Pump?
An ion pump, referred to as a sputter ion pump, is a vacuum pump designed for ultrahigh vacuum conditions. This includes the inducing of ionization on gas particles and the utilization of a metal getter that sputters. Through these actions, it efficiently captures gases, markedly decreasing the pressure within the vacuum chamber. As a result, it fosters exceedingly clean environments, critical in numerous scientific and industrial settings.
Can you provide a brief history of ion pumps?
The inception of ion pumps traces back to Julius Plücker in 1858, upon his discovery of ionization phenomena. A defining moment arrived in 1957 when Varian Associates developed and patented a sophisticated ion pump capable of attaining ultra-high vacuum conditions. This marked a seminal point in the history of vacuum technology, propelling the field forward.
Why are ion pumps crucial in vacuum technology?
Ion pumps are indispensable for establishing and sustaining ultra-high vacuum environments. They are vital in fields demanding pristine, astronautic settings, such as scientific research, molecular beam epitaxy, and semiconductor fabrication. Their precision ensures the absence of contaminants, crucial for the success of these applications.
How does the Penning trap mechanism work in ion pumps?
The Penning trap mechanism integrates magnetic and electric fields to ionize gas particles confined within the vacuum chamber. These charged particles are directed onto a titanium cathode. Once there, they can either undergo burial or participate in chemical reactions that significantly reduce the pressure of the chamber.
What is involved in the ionizing gas particles process?
Ionization of gas particles within ion pumps occurs through exposure to high electrical potentials amidst magnetic fields. This intense environment strips gas molecules of their electrons, converting them into ions. These ions are then effectively captured by the titanium cathode, thereby reducing the gas pressure within the chamber.
What is the sputtering process in ion pumps?
The sputtering process in ion pumps is a method where a titanium cathode is impinged upon with ionized gas particles. As a consequence, titanium atoms are emitted. These atoms interact with gas molecules through reactions or burial, effectively refreshing the cathode surface and maintaining a low-pressure vacuum environment.
What are the different types of ion pumps?
Several ion pump variants exist, including standard diode pumps, noble diode pumps, and triode pumps. Standard diode pumps are versatile, nobel diode pumps excel in inert gas applications, and triode pumps specialize in maintaining stable pumping rates for noble gases. Their variety serves diverse needs within both scientific and industrial settings.
What are some applications of ion pumps?
Ion pumps are fundamental in ultrahigh vacuum systems for both scientific exploration and industrial production. They are pivotal in activities such as molecular beam epitaxy, scanning probe microscopy, and semiconductor manufacturing. Their key role ensures the creation of environments devoid of contaminants, vital for success in these areas.
What are the benefits of using ion pumps?
The advantages imparted by ion pumps include their clean operation characterized by the absence of oil and mechanical parts, negligible maintenance needs, and a performance devoid of vibrations. These features render them ideal for delicate experimental configurations and precise manufacturing processes, offering unparalleled reliability.
What are the challenges and limitations of ion pumps?
Despite their merits, ion pumps face challenges such as inefficiencies in trapping particular gases, like hydrogen and helium. Additionally, they may have constrained capabilities against heavy gas loads. As the getter material becomes saturated, the pumping efficiency for these gases diminishes over time.
How do ion pumps compare with other vacuum pumps?
Ion pumps, when compared to alternative vacuum technologies like turbomolecular, diffusion, and non-evaporable getter pumps, exhibit their unique advantages. For instance, turbomolecular pumps boast rapid pumping rates, diffusion pumps showcase high capacities, and non-evaporable getter pumps excellently pump hydrogen without electromagnetic interference. Each type addresses divergent needs in vacuum systems.
How do you choose the right ion pump for specific needs?
Choosing the right ion pump entails evaluating the need for pressure levels, gas types, and volume of the chamber. Critical factors for consideration include the pump's type, size, and particular configuration. This ensures not only efficiency but also longevity in servicing scientific and industrial applications.
What are some tips for maintaining and troubleshooting ion pumps?
For optimal performance, ion pumps require regular maintenance focused on aspects like monitoring pumping speed and preventing gas backstreaming. Timely resolution of common issues, along with the apt recognition of issues requiring professional intervention, can effectively lengthen the operational lifespan of ion pumps. An informed approach is paramount.
What are the future trends in ion pump technology?
Ion pump technology is poised for advancements that enhance efficiency and capability. Future developments might see the introduction of new getter materials, sophisticated control mechanisms for precision, and synergies with complementary vacuum technologies. The goal is to attain unprecedented levels of pressure reduction and superior pumping speeds, pushing the limits of current ion pump capabilities.
Source Links
- https://en.wikipedia.org/wiki/Ion_pump
- https://www.gammavacuum.com/knowledge-center/theory-of-operation/
- https://www.leybold.com/en-us/knowledge/vacuum-fundamentals/vacuum-generation/pump-typeshow-do-ion-pumps-work